
May 29, 2024
As captured in the popular imagination, the concept of robot assistants conjures up visions of docile mechanized servants, or, at the other extreme, sentient android overlords bent on human destruction. The reality, of course, is a lot more practical. Collaborative robots, more commonly known as cobots, are already making inroads into the industrial manufacturing landscape thanks to a shortage of skilled labor, rising labor costs and increasingly complex logistics and supply chain considerations.
The global industrial cobot market is expected to balloon from $771 million in 2022 to more than $1.66 billion in 2029, according to data from Industry Research, as adoption rates accelerate due to advances in artificial intelligence, digital transformation and a new, post-COVID manufacturing mindset.
What’s often lost in the conversation, however, is how best to incorporate measures that allow humans and cobots to work together safely and harmoniously, in particular as these industrial partners operate in ever closer physical proximity.
The Origins of NexCOBOT
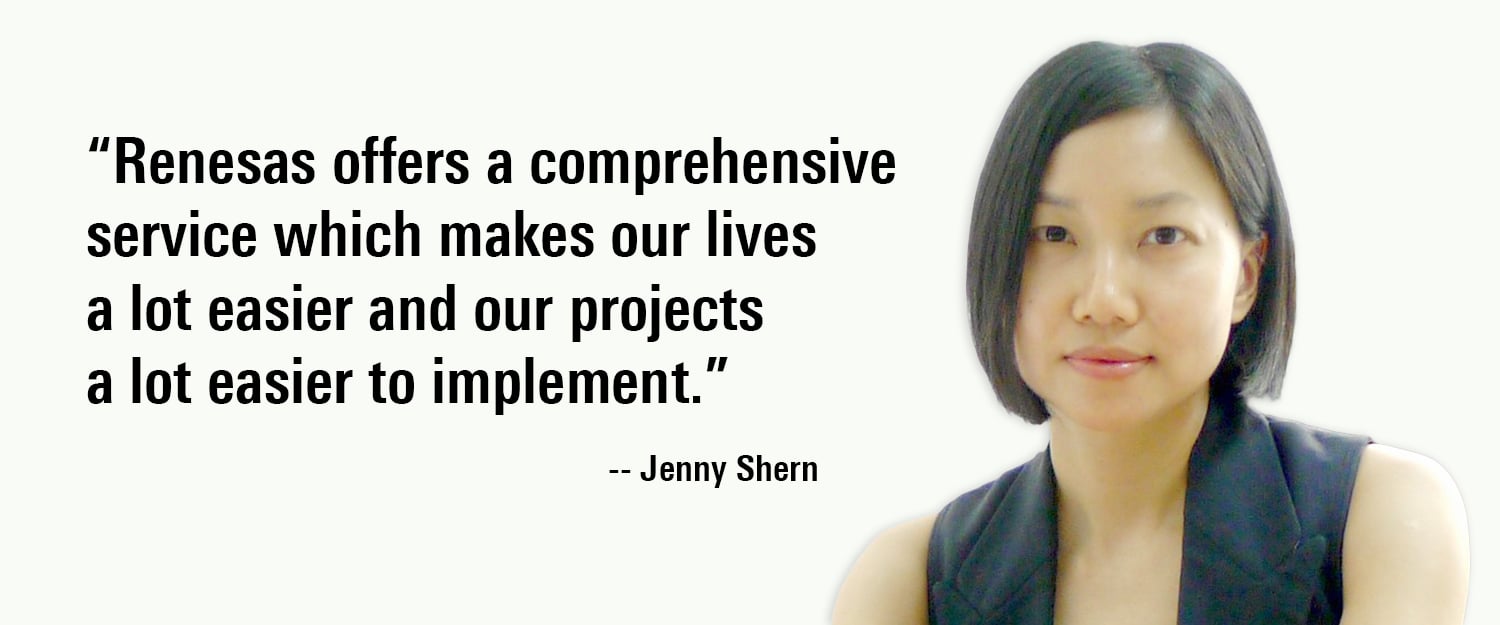
NEXCOM, a leading global intelligent solutions supplier with headquarters in Taiwan, began piloting the concept of cobot systems in 2012 inside the company’s IoT Automation Solutions Business Unit with a roster of industrial automation and software experts dedicated to robotics and machine control. By 2018, the R&D effort – as well as expanding end-market opportunities – had matured enough to warrant spinning off the team into what is today NexCOBOT.
“2018 was when we saw that the trends of smart manufacturing, industrial IoT and robotics were really starting to boom,” said Jenny Shern, NexCOBOT’s general manager. “With the coming integration of AI, the industrial internet of things and robotics, we saw an opportunity to organize our company to focus on what we believe is an important new vertical market.”
With the mothership, NEXCOM, providing a robust industrial PC hardware platform and manufacturing infrastructure, NexCOBOT turned its attention to building a dedicated software development environment and applications engineering team focused on safety protocols.
Educating the Market on Cobot Functional Safety
NexCOBOT initially launched a program to educate network partners, universities and technical colleges with a robot kit and training courses for industrial robotics design. That regional effort laid the groundwork for a global market expansion that today includes a complete industrial control platform with design specifications as well as EMC and signal isolation requirements mapped out for machine builders and robot designers to follow.
NexCOBOT’s FuSA portfolio now extends across a range of hardware, including industrial robot and EtherCAT motion controllers, remote safety digital IOs and software development kits. An expanding array of use cases includes AI-enhanced semiconductor wafer inspection, defect detection, object recognition and conveyor belt tracking working side by side with humans in green-waste recycling applications.
“The initial challenge we overcame was to find the right way to offer our product series in a modularized format,” Shern said. “Some of our customers need hardware design expertise. Some of them just need the software piece. Others require hardware plus integrated software design, while still others need documentation, functional safety training and consulting services. With this comprehensive approach, we’re able to offer an open platform and the flexibility and scalability of a modularized design.”
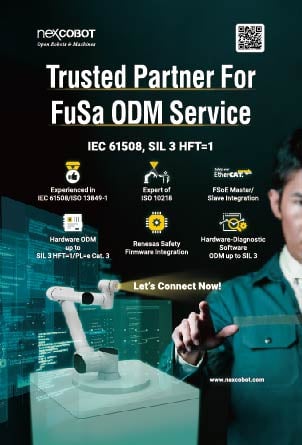
Functional Safety Takes a More Prominent Role in Cobot Design
In the early days of NexCOBOT, functional safety (FuSa) was more of an afterthought for industrial manufacturers. As the sector began to become more heavily automated, however, standards and regulatory bodies such as ISO began looking more closely to ensure a safe industrial operating environment. NexCOBOT was in the right place at the right time.
“In the very beginning, there were few requirements,” Shern said. “Some of our customers were aware that new ISO safety standards for industrial robots were coming, but it wasn't very prevalent at that point. At the same time, though, we had an innovative program with a partner in Germany to release a complete functional safety solution. So, we were ready, and as we moved along we saw more and more customers asking for our solutions.”
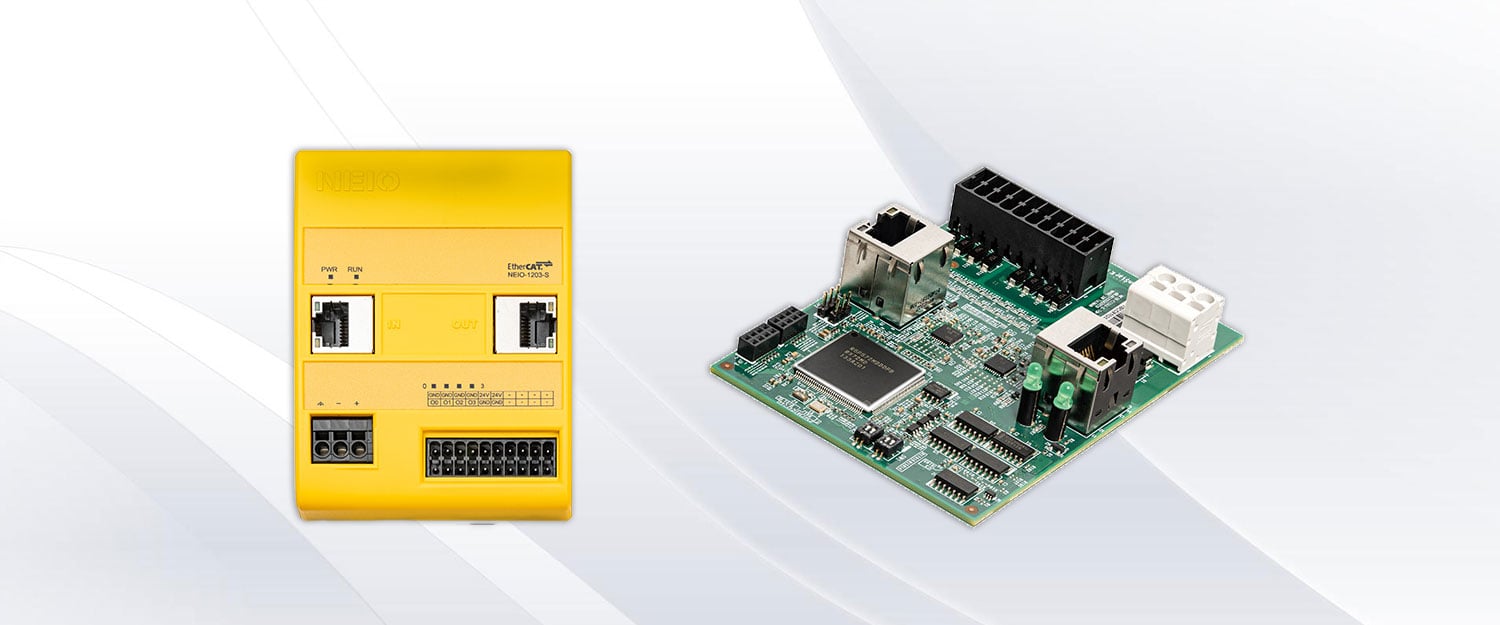
Renesas Technology Helps Accelerate FuSa Adoption
NexCOBOT began working with Renesas in 2022 to design a digital safety IO interface and has since adopted Renesas RX MCUs and RZ MPUs as well as pre-certified FuSa solution kits and self-test libraries. While industrial systems typically entail a longer design process than the consumer market, Shern said customers are now asking for greenfield FuSa designs and working prototypes faster than ever. Renesas’ one-stop functional safety solution for general-purpose processors is responding to the challenge by helping NexCOBOT reduce FuSa development by as much as two-thirds – from six years to two.
“We found that Renesas provides a very complete, comprehensive FuSa solution for embedded systems,” Shern said. “Usually, if you look at FuSa for embedded systems, customers are going to one vendor for a hardware chipset, another for the real-time OS software and a third for the full safety library. It quickly becomes a pain to integrate all of these bits and pieces. Renesas offers a comprehensive service which makes our lives a lot easier and our projects a lot easier to implement.”
We look forward to our continued collaboration with NexCOBOT to advance industry safety standards and foster deeper – and more productive – working relationships between humans and robots. Together we are enabling a new era in advanced industrial automation.