The concept of Industry 4.0 involves integrating intelligent machines, systems, personnel, and deriving changes in manufacturing processes. The aim is to boost work efficiency and personalize production, allowing for flexible assortment alterations. In addition to technological enhancements, Industry 4.0 applies new ways of working by defining the role of people. Computerization, connectivity, and AI integration maximize labor safety and efficiency. Especially, the industrial network is the key to connectivity among different levels of the industry infrastructure. Industrial networks provide instantaneous data access on a factory floor by exchanging information amongst field devices with the following supporting goals:
- Connectivity and interoperability among multi-vendor systems and (or) devices for adaptability and ease of expansion.
- Integrity and security of data in transmission and access to databases for reliable factory operation.
- Minimum possible delay or latency in transmission for timely analysis and decisions.
- Integration of voice, data, and video-image transmission to provide consistency of information.
In order to define and standardize the operation of a device's equipment connection to a network, the Open Systems Interconnection (OSI) model was developed in the 1980s. The OSI model has seven layers, each with a unique purpose. As shown in Figure 1, each layer works with the layer above and below to enable end-to-end communication between systems or networks. Information from an Application (specified at the topmost or Application Layer) is consistently packaged and distributed via a range of physical networks (defined at the bottommost layer) through the interdependence and mutual service of seven layers.
Figure 1. OSI Layer
The industrial communication network is an essential component of an industrial system since it enables a single control unit to manage many I/Os across a network, regardless of the technology. A factory's networked control architecture may have motor control, motion control, robotics, and traditional programmable logic controllers (PLC). As shown in the figure below, the primarily used industrial network technologies are Industrial Ethernet (EtherCAT, Profinet, EtherNet/IP, CC-Link IE, Modbus-TCP, POWERLINK, Sercos III, OPC-UA) and Fieldbus (Profibus, Modbus RTU/ASCII, DeviceNet™, CANopen, Asi-5, IO-Link). In industrial automation, objects are controlled via PLCs, SCADA, and DCS. Field instruments, smart field devices, supervisory control PCs, Remote I/O, and human-machine interface (HMI) systems are available. To connect and communicate, these devices require a robust communication network strategy. They connect field equipment, controllers, and PCs so that data and control signals may be sent wirelessly or via cable. Similarly, A sensor network, which comprises a group of small, powered devices, and a wireless or wired networked infrastructure, record conditions even in case of harsh factory floors. Sensor network nodes cooperatively sense and control the environment and enable interaction between M2M (Machine-to-Machine), H2M (Human-to-Machine), or vice-versa.
Physical Layer | Protocol | Protocol Description | Information Network | Controller Network | Field Network | Sensor Network |
---|---|---|---|---|---|---|
Industrial Ethernet | EtherCAT® | Need specific hardware (HW) to have Vendor ID assigned by ETG, user can get Vendor ID for FOC | ✓ | ✓ | ||
PROFINET® | 2 major classes, RT: developed by SW basis, IRT by Specific HW, PI organization manages Profinet, Profibus, and test labs for certification | ✓ | ✓ | |||
EtherNet/IP™ | Developed by SW basis, ODVA manages EtherNet/IP, DeviceNet and test labs for certification | ✓ | ✓ | |||
CC-Link IE | Need specific HW for CC-Link device, Wide bandwidth for 1G bps | ✓ | ✓ | |||
POWERLINK | CANopen communication profile, suitable for applications with hard real-time requirements in µs range. | ✓ | ✓ | |||
Sercos III | High synchronization. For motion control | ✓ | ✓ | |||
Modbus/TCP | Technical development by Modicon now owned by Schneider | ✓ | ✓ | |||
OPC-UA | M2M communication protocol for IA developed by OPC-UA Foundation | ✓ | ✓ | ✓ | ||
Fieldbus (Serial communication) | DeviceNet™ | Technical development by Allen-Bradley, now owned by Rockwell | ✓ | ✓ | ||
Modbus/RTU, ASC II | Refer to Modbus/TCP | ✓ | ✓ | |||
PROFIBUS | Refer to PROFINET | ✓ | ✓ | |||
IO-Link | Dedicated connecting digital sensors and actuators | ✓ |
Market trends in equipment used in the Information network and Control Network layers have shifted from serial connection like CAN or RS-485 to Industrial Ethernet. Market requirements also changed to more real-time operations to connect with other layers and manage big data as central management. Ethernet connectivity is becoming increasingly popular in the industrial sector, which is allowing for the development of new methods for improving efficiency and dependability in manufacturing processes. Ethernet has slowly but steadily replaced traditional communication protocols in the industrial/operational technology (OT) setting, where it is used for machines, robots, and other industrial automation applications. Compared to more conventional fieldbuses, Ethernet can offer more reliable and secure services, so its use is on the rise. To increase productivity, yields, uptime performance, product quality, and overall profitability, OT environments of all types are integrating machines, robots, and other crucial pieces of automation equipment in novel ways by taking advantage of Ethernet-enabled capabilities and more. Original Equipment Manufacturers (OEMs) can differentiate themselves from the competition and better meet the needs of their target customers by making use of Ethernet ports, sensors, devices, and other enabling components. Since Ethernet can communicate instructions in millisecond-accurate fashion over long distances, it could eventually allow factories to run almost entirely without human intervention. Ethernet's speed and bandwidth allow for the unprecedented collection of massive amounts of real-time data. Industrial Ethernet facilitates long-term cooperation and success by letting machine manufacturers and users work together on network design and planning. Due to the same, new opportunities are developing that keep them commercially engaged. Due to Ethernet, remote access to diagnostic and status data is quick and easy. End users may have rapid access to the greatest machine diagnosticians on the global team that created the equipment—without the downtime or cost of an emergency. Redundancy and determinism are important factors when defining Industrial Ethernet where it leads from its intranet. In short, Industrial Ethernet is better suited to handle plant noise, plant process needs, and harsher environments, and is even able to respond better to data collisions on the factory floor with optimized reliability and security.
One of the major benefits of Ethernet is that the Ethernet protocol can manage high-speed industrial processes, for instance, the desired hand-off decisions between machines in an assembly line, down to milliseconds or even to nanoseconds, in a consistent and repeatable manner. Here, the deterministic nature of Industrial Ethernet provides a good platform for future industrial network applications such as Time Sensitive Networking or TSN. Some of the key features of the same are narrated in Figure 2.
Figure 2. TSN features
Figure 3. IT-OT convergence drivers
On the factory floor, TSN (defined by the IEEE 802.1) type of deterministic Ethernet framework provides benefits of various TSN protocol features such as time synchronization, frame preemption, ingress policing, time-aware shaping, and many more. Cyber-physical systems are central to Industry 4.0. These systems require cyberspace representation. For that, the operations technology (OT) and information technology (IT) networks from the upper factory layers must converge. This can be realized using techniques such TSN, AI/ML-based auto reconfiguration of the network. However, TSN protocols as well as network auto reconfiguration are still in an evolving stage that will share the future of industrial applications.
Seamless real-time communication is the core prerequisite for all Industry 4.0 and Industrial Internet of Things (IIoT) implementations. Renesas offers best-in-class communication components for all leading Industrial Ethernet and Fieldbus communication protocols, such as EtherCAT, PROFINET, EtherNet/IP, Modbus, CC-Link, and more. All of these solutions come with comprehensive software support. For example, R-IN32M3 is a Certified Multiprotocol Industrial Ethernet Solution (PROFINET, EtherNet/IP, and EtherCAT, etc.) is a certified hardware and software solution that speeds up product development and brings it fast to the market, Figure(s) 4-5 corresponds the same.
R-IN32M4-CL3, the next level of R-IN32M3, for Industrial Ethernet (IE) communication heralds support for CC-Link IE Time Sensitive Networking (TSN), a communication standard for next-generation Ethernet TSN technology. Similarly, RZ/T2M, RZ/N2L, the latest MPUs have integrated time-sensitive networking (TSN) compliant three-port Gigabit Ethernet switch and an EtherCAT slave controller which support industrial network communication protocols, including EtherCAT, Profinet IRT/RT, EtherNet/IP, and OPC UA.
In addition, Renesas RX72M (high-performance 32-bit microcontroller) based networking solutions that are designed to reduce the development time when using RX72M for slave equipment for industrial networks, are available for motor drives at robot terminals, small programable logic controllers (PLCs) and remote I/O, etc.
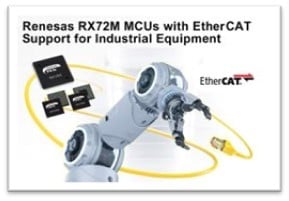
Figure 6. RX72M
Figure 7. RX72M Industrial Network Solution
The RX72M Network Solution consists of an RX72M-based evaluation board along with sample software for the OS, middleware, and industrial network communication protocols supporting about 70% of the major industrial network communication protocols in the market, which strengthens our competitiveness in the development of our customers' products. The RX72M solution (inc partner MW) is designed to address a wide range of Industrial Ethernet protocols, including OPC UA, EtherCAT, PROFINET RT, EtherNet/IP, Modbus TCP, etc., giving flexibility and multiple networking options for industrial designs.
Renesas offers a range of MCU/MPU devices to support one-protocol and multi-protocol communication options, as well as various Factory Automation use examples. One protocol-based devices give customers a compact footprint and inexpensive cost, whereas multi-protocol-based devices provide a unique environment. Renesas Industrial Ethernet MCU and MPU devices offer redundancy and enable the development of custom-specified products. Renesas Industrial Ethernet-enabled MCU/MPU devices make it possible to leverage any layer of communication. Some of our multi-protocol devices can simultaneously run two industrial protocols. So, customers can develop the gateway between Industrial Ethernet protocols, making Renesas an ideal choice for developing robust industrial networking solutions.
Previous blog posts: