The IoT system utilizing sensing data has been increasingly introduced to the manufacturing and infrastructure industry fields. The aim of the IoT system is to create new value by acquiring and utilizing huge data by IoT. In the IoT system, the DAQ (data acquisition) is responsible for acquiring sensing data. With the evolution of the IoT system, the DAQ is also evolving by increasing the number of channels to be measured and adding industrial network functions, etc. Though, it is said that only a few percent of the acquired data are utilized. One of the reasons why data utilization is not fully used is that data analysis cannot catch up with the increasing amount of data. As shown in the figure below, the host MCU in the existing centralized system is busy with digital signal processing and has no room to analyze the increasing data, like the comparison of multiple sensor signals. Data utilization does not proceed unless data is analyzed.
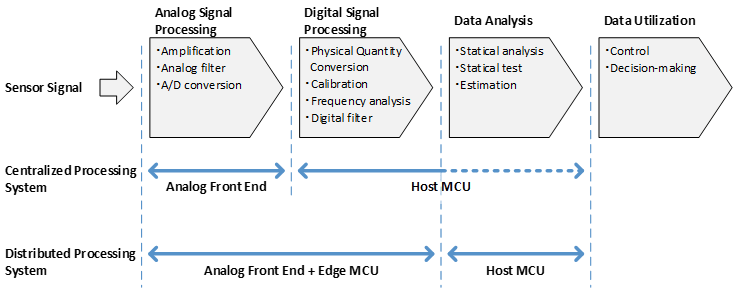
To address this challenge, Renesas is focusing on distributed processing/edge computing. In this context, distributed processing/edge computing means that the edge acquires the data and processes the digital signal to make the data analysis easier. By performing digital signal processing on the edge side, the host MCU doesn’t have to allocate resources to it and can perform more advanced data analysis work. Thus, data utilization can be expected to progress. In addition, it is also possible to reduce the pressure on communication and storage.
As an example of distributed processing/edge computing, Renesas has provided a reference design for a multi-channel isolated analog measurement system targeting DAQ-related applications such as recorders and analog input modules. This reference design consists of four RX23E-A/1unit placed on the edge side and a host MCU using RX72M.
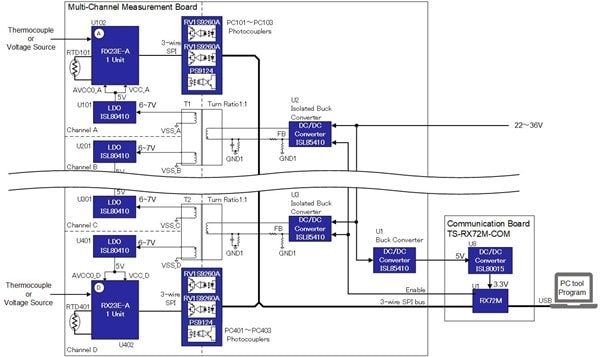
RX23E-A/1unit performs digital filter processing and conversion of a physical quantity in addition to A/D conversion, leveraging its strength of integrating MCU and high-precision AFE into a single chip. This allows RX72M to perform advanced data analysis that only a host MCU can do, such as comparing the data acquired from each edge.
Some applications require the synchronization of the measured data and the step response time. In this reference design, 4-channel synchronous measurement can be realized within 1msec. The step response time is 70msec for 10msec of the data sampling cycle. These specifications appear to be adequate for the system that processes sensing signals such as temperature or pressure.
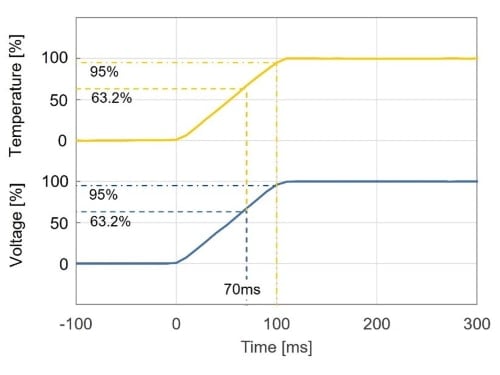
This solution has been published on the web as an Application Note, “RX23E-A Group Channel-to-channel isolated analog measurement system” (Document No. R01AN5679EJ0110). It is also introduced on the specific web page. Please feel free to check it out.