General Introduction
Actually, there is no clear scientific definition of “Artificial Intelligence (AI)”, but one common understanding is to interpret AI as learning systems that are observed by humans as “intelligent”. A more definite description is difficult to achieve since the term “intelligence” already lacks a clear rationalization.
Concerning Automotive applications, representative and mostly known AI-related functions in today’s and future cars include Automated Driving (AD) applications in terms of object sensing, object recognizing and deciding about resulting reactions. Such applications are usually associated with very high computing performance in the ~100k DMIPS range.
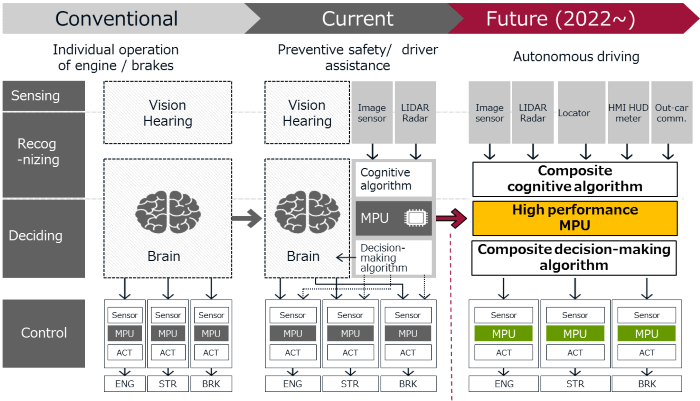
The lower application layer, which is concerned with conventional real-time actuator control in terms of “vehicle motion” activities like propulsion, steering and braking, may on a first glance not be a main target to gain from the new hype of the AI and ML technologies. It would seem that for today and most likely in the future, this layer will continue to be realized with regular microcontrollers having limited embedded performance (up to 10k DMIPS), due to everlasting cost pressure.
However, exactly the opposite is true!
The real-time actuator control applications of the “vehicle motion” categories are especially challenged by various new requirements (e.g., EURO7 legislation) that lead to increased algorithm complexity and generate the need for much higher performance levels and larger communication bandwidth. All this will be made possible without a mentionable cost adder – which is very typical for automotive control applications.
How will the much higher performance requirement for AI and ML functions with conventionally cost-balanced MCU systems be realized? The answer lies in specialized hardware (HW) accelerators which are implemented as co-processors embedded within the MCU silicon.
The RH850/U2B Microcontroller with Embedded HW Accelerators
Renesas’ HW accelerator concept for its next-generation 28nm microcontroller, the RH850/U2Bx- FCC, is the “DFP” (Data Flow Processor) IP known as the “DR1000C”, licensed from NSITEXE, Inc. of Japan. NSITEXE is an IP vendor, established in 2017 as a spin-off from DENSO Corp., specializing in the development of advanced processors.
The RH850/U2B FCC microcontroller targets the application areas of vehicle motion and zone-control, realizing up to 8 performance cores running at 400MHz each with virtualization support and Quality-of-Service (QoS), solving the challenge to integrate multiple applications into one device while granting Freedom-From-Interference to meet the ISO 26262 ASIL-D standard.
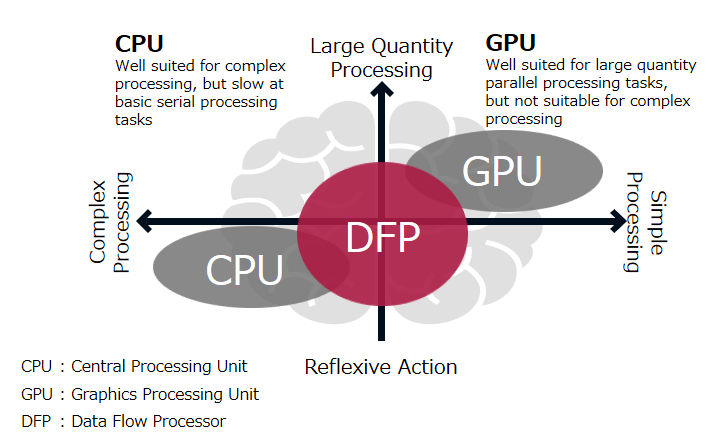
The DR1000C is a dedicated RISC-V based parallel coprocessor, optimally designed for multithreading mechanisms and vector instructions to offload intensive computing tasks from the main CPUs with the target to accelerate advanced control algorithms.
Conceptually, the DR1000C is a Multiple Instruction Multiple Data (MIMD) high-performance ASIL-D vector processor, achieving both data-level as well as task-level parallelism. The combination of a Vector execution unit with a multi-threaded architecture realizes high flexibility to accelerate a wide range of algorithm types that are typically used for AI and ML functions. Refer to the “use case” section below for more details.
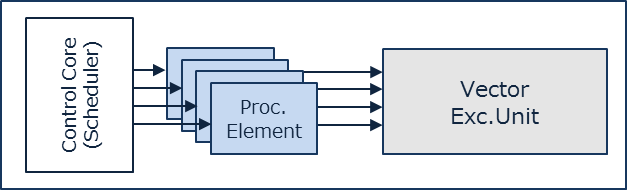
DR1000C Performance
The specific parallel MIMD architecture of the DR1000C IP results in a performance advantage in an order of magnitude compared to a conventional automotive CPU (i.e. Harvard architecture). Specific mathematical functions, like a Gaussian Process (Radial basis function), Kalman Filter or BLAS strongly benefit when executed with the DR1000C.
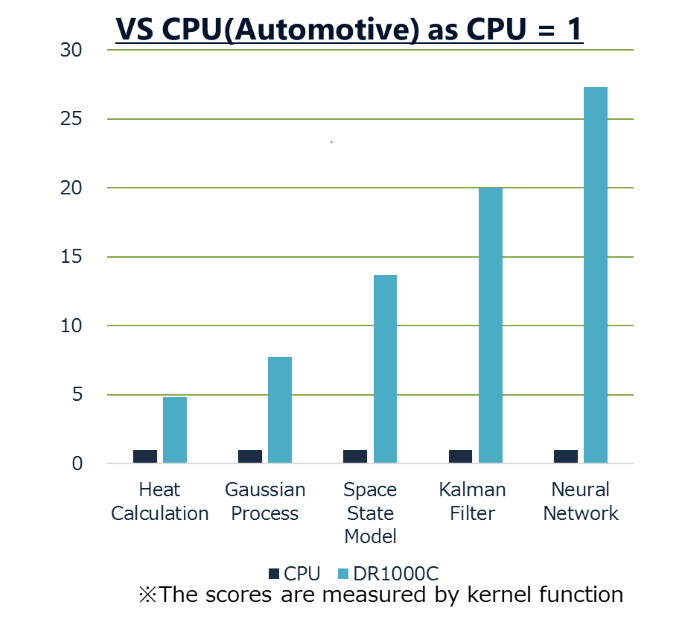
Use Cases
There are multiple use cases in the automotive context of AI or ML that would benefit from the DR1000C. The following are a few application examples out of the “Vehicle motion” segments mentioned beforehand.
Virtual Sensor: This is a concept to replace a physical HW sensor by virtually processing a real-time model to emulate the physical processes of the related real-world system. The simple motivation here is system cost reduction. The underlying modeling approach often uses a radial basis function network which can be interpreted as an artificial neural network. Radial basis functions have many use cases, including approximation of functions, predictions of time series, and system control.
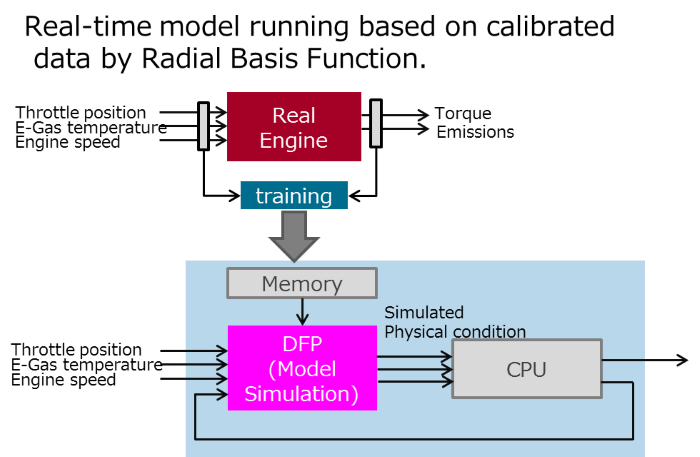
Model Predictive Control (MPC) is a methodology to control power converters or electric motor drives. It provides the capability to handle a large variety of control tasks by dynamically predicting and optimizing system parameters next to the incorporation of system constraints. Non-linear MPC models especially may be reflected in the form of a trained data set (based on artificial neural networks).
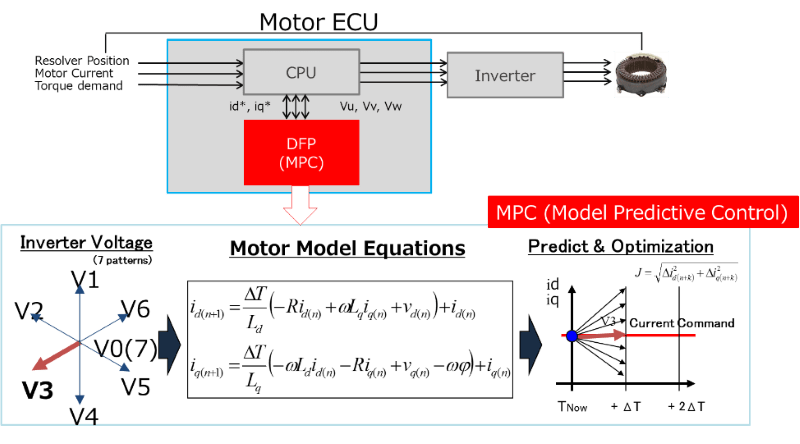
Gateway Intrusion Detection System (IDS)
An IDS is supposed to identify network attacks by comparing “normal” activity against the actions of an intruder. Today, mostly rule-based systems are used to identify known attack types, which are less successful when an attack uses different or so far unknown methods.
Here, Machine Learning provides an extended possibility to classify network activity based on traffic patterns including bandwidth, devices, ports, and protocols. By comparing the trained (machine learned) patterns of “healthy” traffic with the actual network communication, the detection of newly evolved threat types can be achieved. This is something a static rule-based system is not capable of doing.
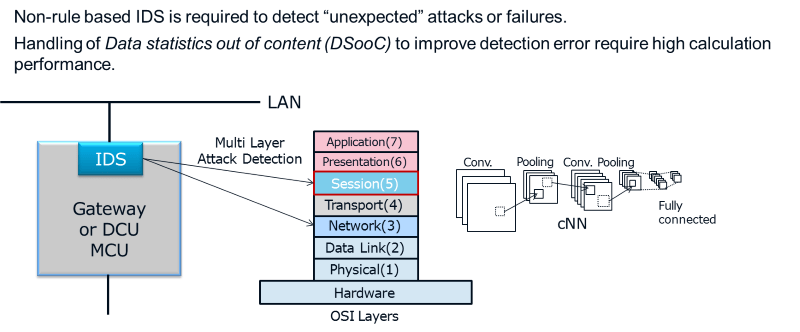
DR1000C Tool Environment
The application development can be realized by C-coding where user applications are written in C combined with intrinsic functions to call DR1000C services. Alternatively, model-based development in terms of a “DFP toolbox” for MATLAB/Simulink will also be available. An “SDK” will comprise a Run-time Thread Scheduler (RTS), a GNU-based toolchain, a simulator, and a debugger. Optionally, Functional Safety in terms of ASIL-D capable diagnostic libraries as well as ISO26262 tool qualification are under development.
Conclusion
In the near future, cost-balanced automotive MCU systems must be able to cover a wide range of algorithms, especially Machine Learning (ML) and embedded Artificial Intelligence (AI), control theory, signal processing, and physical modeling.
Renesas will enrich the next-generation microcontrollers with the flexible HW-accelerator concept “DR1000C” which is optimized for automotive use cases and can boost the conventional MCU real-time performance by decimal factors while keeping the respective cost and power dissipation footprints at an affordable level.