My name is Tsuda from Renesas and this is my second blog post, you can read my first blog here.
Renesas offers an in-vehicle grade multi-cell lithium-ion battery control system evaluation kit (ISL78714BMS5XBEKIT1Z, ISL78714XB-EVKIT1Z) and is considering a wireless battery management system.
I am involved in the development of sample application software and models for battery control system evaluation kits, and sample application software for PoC (Proof of Concept) models of wireless battery management systems.
In this blog I will explain the trends, challenges, and solutions for battery management systems facing an increasing number of battery cells.
Battery Pack and Battery Management System
The battery pack provides the power for the EV and consists of multiple cells. The cell voltage is a few volts and the pack voltage is several hundred volts, comprised of multiple cells in series. For example, 1-cell’s voltage is 3.5V, and a pack consisting of 96 series connected cells produces a pack voltage of 3.5 * 96 = 336V.
The battery management system monitors the cell voltages, pack current, and temperatures; it performs cell balancing by equalizing the voltages of each cell, and it switches the battery pack to the charger or inverter using contactors. The battery management system not only controls the battery but it calculates the battery charge/discharge, state of health, and much more, all based on the monitored values.
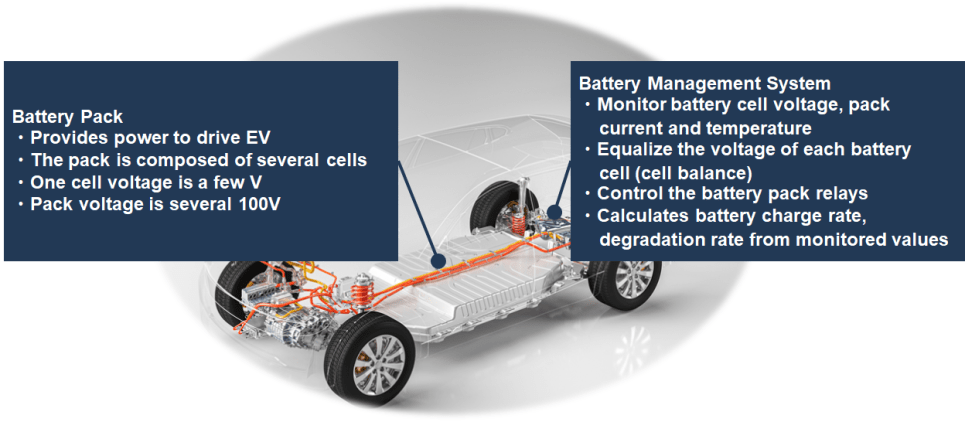
Battery Trends
There are two major trends in battery technology today. The first is to increase the capacity to extend the driving range. The other is increasing pack voltage for high efficiency. From the viewpoint of the number of cells, increasing the capacity increases the number of cells in parallel, and increasing the voltage increases the number of cells in series.
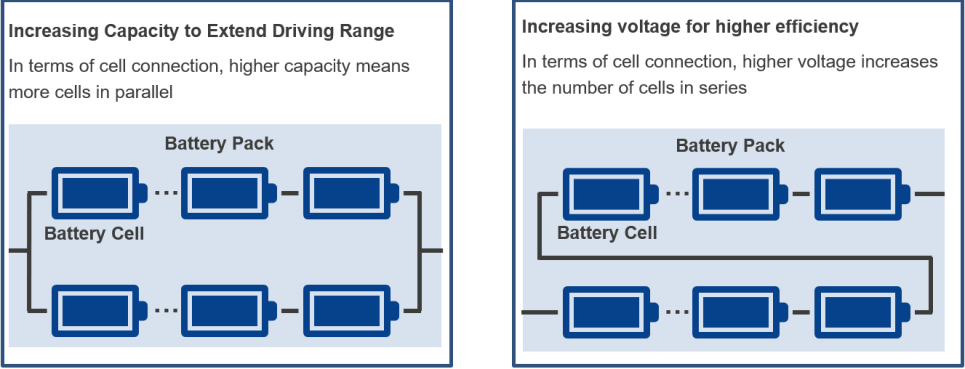
Leading edge battery packs are being split into banks that are connected in series for charging and in parallel driving, optimizing the pack performance but still increasing the cell count. Based on these trends, the number of cells in the battery pack will continue to increase.
Battery Management System Trends
As the number of cells in the pack increases so does the number of cell monitors because the number of cells that can be connected to a cell monitor is limited. This increases the number of wires and connectors between the cell monitors.
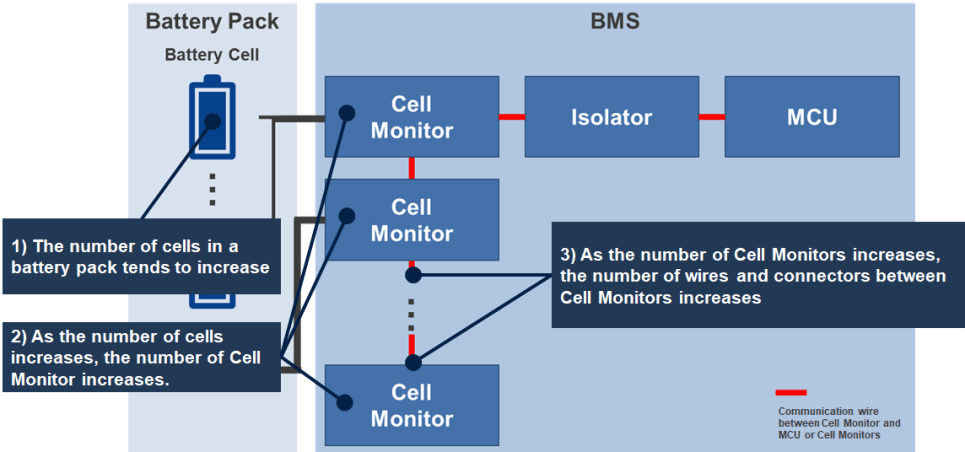
Issues of Battery Management System
When the number of wires and connectors between cell monitors increases, there are two challenges. One is layout changes such as split packs increase wire length, cost, and weight. The other is an increase in failures such as wire breaks and poor connector contact.
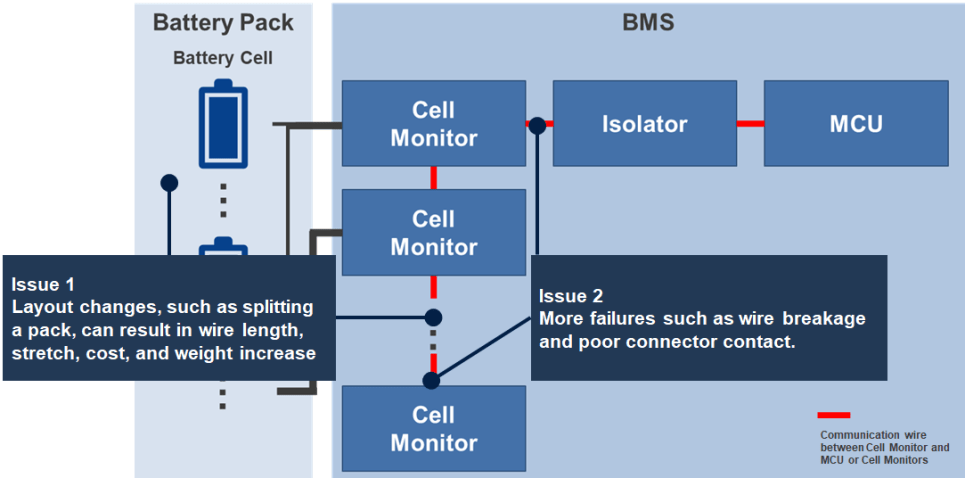
Measures for Battery Management System
I am working on changing the communication between the microcomputer and cell monitor from wired to wireless as a countermeasure for the two issues.
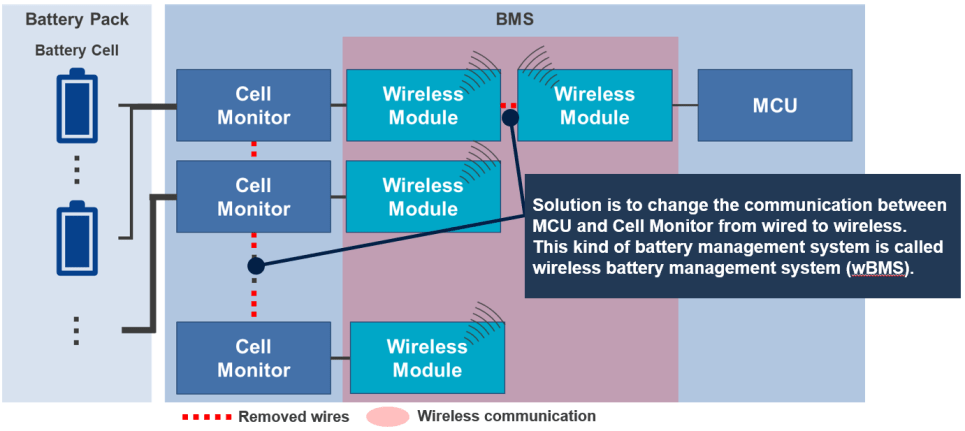
A battery management system like the one above is called a Wireless Battery Management System (wBMS).
Which wireless standard is better for a wireless battery management system? In terms of communication distance, wireless communication is classified into short-range wireless communication, PAN (Private Area Network), LAN (Local Area Network), MAN (Metropolitan Area Network), and WAN (Wide Area Network). Of these, wireless battery management systems are classified as PAN. There are multiple wireless standards for PAN. For example, ZigBee, Bluetooth®, and Bluetooth® Low Energy (BLE). Of these, I believe BLE is the most suitable for a wireless battery management system from the perspective of communication speed and power consumption.
Based on the above, I believe that the wireless battery management system will have the following configuration.
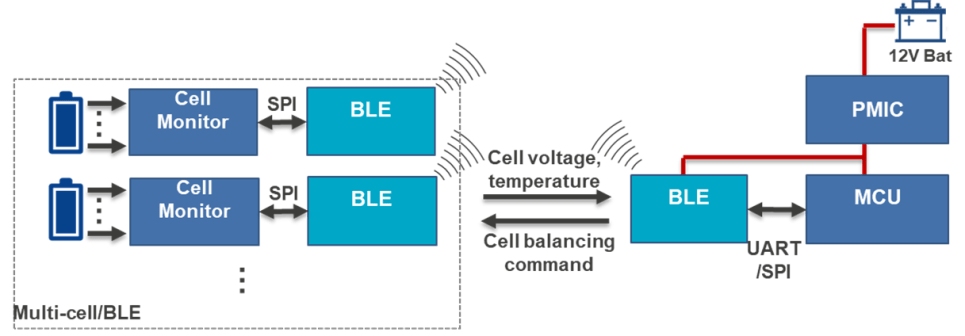
For more information please see wireless battery management system.
I am currently writing PoC software for the system above. One of the issues I encountered during the PoC development was the communication time between the MCU and cell monitor. I hope to explain this issue and solutions for it in more detail in my next blog or demo.