Advantages Provided by DRP
Are you facing these challenges with embedded system development?
- Want to shorten the development cycle
- Want to be equipped with the latest algorithm ahead of other companies
- Want to support the repeated specification changes of complicated algorithms
- Want to add functionality after the product has shipped
DRP solves such device development issues
DRP shortens the development cycle
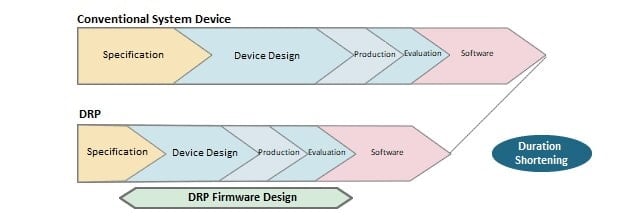
In conventional system design, device design could not be started until the specifications were fully determined. With DRP, you directly design the hardware (DRP firmware design). Because you can start producing the device before the specifications are determined, this can shorten the development cycle.
Build a flexible system
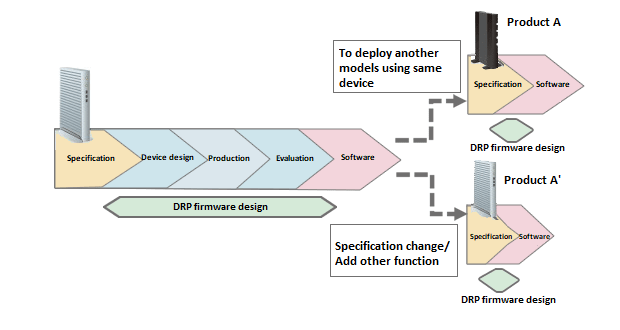
The flexibility that DRP provides enables continuous added value by software update. After the product is shipped, specification changes and additional functions can be implemented via software update. In addition, using the software library of DRP firmware which has already been developed makes it easy to deploy to other products that use the same device.
Implement complicated algorithms and improve performance with ease
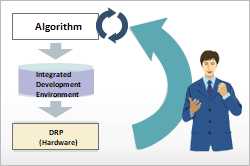
The algorithm designer can build firmware with an algorithm written in C in an integrated development environment, implement this firmware in DRP to make it hardware, and run it on an actual machine. Thus, since algorithm designers can implement, evaluate and modify their algorithm on an actual machine by themselves, development time and performance can be improved significantly.
DRP Features
DRP is programmable hardware which has both the flexibility of software and the speed of hardware. The firmware that defines processing, can be rewritten on the go. We suggest the solution of "C-based design + high-level synthesis + DRP" as a way to quickly produce hardware for advanced and complicated processing.
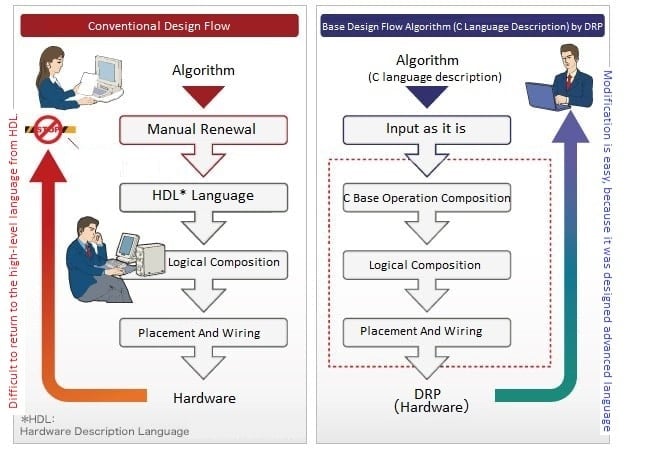
Conventional Design Flow
An algorithm is first developed in C, which is then replaced with hardware description language (HDL) in order to implement it in hardware. This method has the following issues.
- Man-hours required for rewriting - High hurdle between software and hardware
- Technical hurdles - Difficulty of converting highly abstract C language to HDL
- Manual reversion due to specification changes or defects - When a malfunction is discovered after the algorithm has been converted to HDL, investigating the cause at the C language level is difficult
C-Based Design Flow by DRP
With an integrated development environment, complicated algorithms that were conventionally difficult to make hardware can now be converted to DRP firmware for hardware implementation. The algorithm designer can personally evaluate and modify an algorithm on an actual machine, significantly improving the development cycle and performance.
Directly design hardware in C. This is how programmable hardware (DRP) breaks through the conventional concept of designing hardware from C via HDL.