- Blog 1: Standardization Within The Same Product
- Blog 2: Standardization Across The Different Products
The benefit of component standardization is to reduce not only the component cost but also the maintenance workload in the future. In particular, the industrial sensing equipment, which is the main target of the RX23E-A 32-bit microcontroller (MCU), offers a long product lifecycle and diverse specifications, so we could say that the benefit of standardization is even more significant.
There are generally two directions for standardization. One is between models of a product, which I described in the previous blog. In this second blog, I will introduce examples of standardization across the different products with RX23E-A MCU.
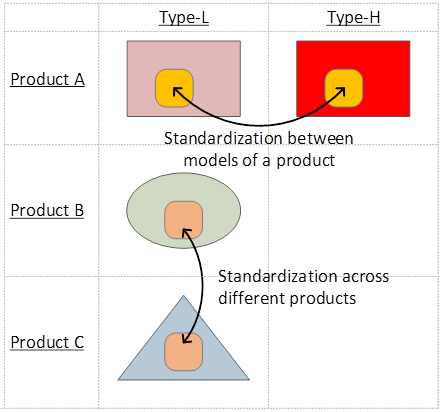
You might hear widely that standardization across different products is difficult. It is mainly due to the cost structures and required function/performance variation among products. Therefore, the component adopted for standardization may not always be the most suitable for the product, which is the root of designer’s concern.
With that premise I will introduce some examples that the RX23E-A has contributed to solving such difficult situation.
[ Example 1: Pressure Gauge and Thermometer]
The first is an example of standardizing between a pressure gauge and a thermometer.
Temperature and pressure are physical quantities that are measured most frequently in industrial applications. Particularly, pressure gauges are used in numerous ways since they could be applied to flow and level measurement as well. Therefore, many manufacturers implement both thermometers and pressure gauges.
Thermometers and pressure gauges are similar in terms of handling minute signals, yet different in terms of required circuit functionality.
Temperature sensors mostly used in thermometers for IA application are thermocouple and resistance temperature detector (RTD). RTD has 2-wire, 3-wire, and 4-wire configuration.
Pressure sensors used in pressure gauges have various type, such as resistive, capacitive, and resonant types and the resistive type is primarily used. And this is the type that RX23E-A could measure. There are several manufacturing methods for resistance type, such as semiconductor method andmetal thin film method and foil strain gauge method but they are common in that they apply resistance bridge.
The RX23E-A has contributed to the standardization of a thermometer and a pressure gauge that are required to support such a variety of sensors. The RX23E-A has full set of functions required for temperature and pressure measurement, including excitation current source (IEXC), bias voltage generator (VBIAS), reference buffer (RBUF), low-side switch (LSW). A thermometer and a pressure gauge can be standardized by utilizing these functions as shown in the figure below.
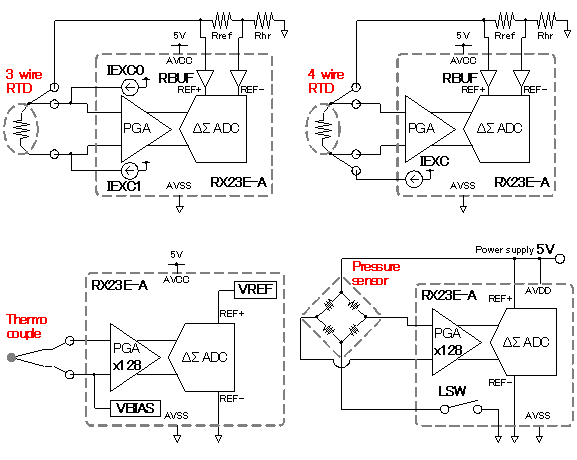
[ Example 2: Portable and Stationary Sensor ]
The second is an example of standardizing a stationary sensor and a portable battery-powered sensor.
Portable battery-powered sensors require lower power consumption. On the other hand, stationary sensors require higher precision and faster performance than portable sensors in most cases. The noise and speed performance of the ADC and amplifier is proportional to the current consumption of the device. Therefore, to address low power consumption and high precision and speed performance, generally different devices are adopted.
To standardize a stationary and portable sensor that has such a contrary requirement, the RX23E-A has an advantage. The delta-sigma ADC built in the RX23E-A could achieve both excellent noise performance in normal mode and low power consumption in low-power modes. The current consumption is about 1mA in normal mode while it is about 400uA in low power mode. By selecting the low power mode appropriately, a stationary and a portable sensor can be standardized as below.
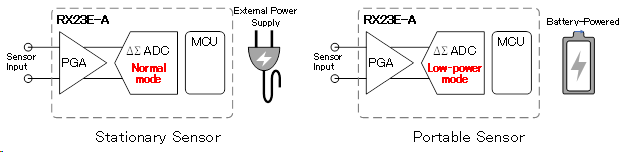
[ Example 3: Indicator and Built-in Amplifier Sensor ]
The third is an example of standardizing an indicator and a sensor with a built-in amplifier. First, I will give you a brief explanation of indicators and sensors with built-in amplifiers.
Depending on the measurement target, sometimes it is impractical to place a large-sized sensor, for example when the space is narrow, or the target has strong vibrations. In such a case, a sensor is placed near the measurement target, and an indicator is placed at a distance. When using a sensor and an indicator together in such manner, there are two configurations for the sensor side and indicator side as below.
- Separated Amplifier Configuration: Only a sensor element or a sensor assembly is on the sensor side, and necessary signal conditioning is performed on the indicator side.
- Built-in Amplifier Configuration: A signal conditioner is built on the sensor side, and signal conditioning is performed on the sensor side as well.
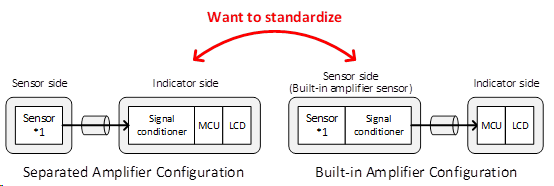
*1: Sensor in this context means a sensor element or a sensor assembly without an electronic circuit.
As shown in the sensor side of the right figure, a built-in amplifier sensor incorporates both sensor and signal conditioner. Since an identical sensor is often used in both separated and built-in amplifier configurations, it is natural to have a demand for standardization.
When standardizing, the challenge is which is suitable components for the built-in amplifier sensor. For built-in amplifier sensors, it is necessary to implement electronic components into a limited, small space. The ideal implementation is that not only analog components like operational amplifiers, but also digital components are implemented to send digitalized signals to the indicator. By sending digitalized signals, built-in amplifier sensors are free from disturbance noise, which often is a problem for separated amplifier sensors. In fact, because of space-constrained, only limited analog components like operational amplifiers are implemented in many cases.
The RX23E-A has solved this space-constrained problem as well as contributed to standardization. The RX23E-A is equipped with high-precision 24-bit delta-sigma ADC and MCU on a single chip in a small package. Therefore, it can be used not only for a signal conditioner of the built-in amplifier sensor but also for a signal conditioner and MCU function of the indicator. As a result, an indicator and a built-in amplifier sensor can be standardized by the RX23E-A as shown in the below.
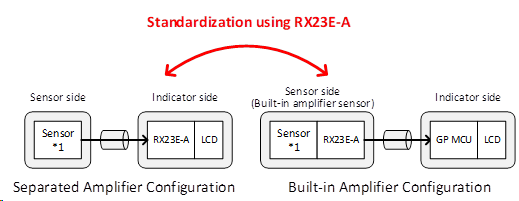
These are three typical examples I have observed.
Difficulty in standardization is to balance between commoditization and differentiation. Standardization leads to commoditization in the end, and we might fail to meet the flexibility of market demands. While we would like to select components with enough margin in the specification for standardization, over-specification components might increase the cost. It is a difficult problem how to balance both. RX23E-A provides the following lineups so that customers can meet various demand flexibility.
- Delta-sigma ADC unit: 1-unit and 2-unit version
- Operating temperature range: -40 to 85℃, -40 to 105℃
- Package: 48-pin QFP, 40-pin QFN
- ROM/RAM: 256KB/32KB, 128KB/16KB
I hope these RX23E-A features will enable differentiation as well as standardization in your application.