Electric motors have shaped the world and continue to do so, at every level. Ranging from small motors that can be found around the home, to heavy-duty industrial motors. With increased awareness of the cost of energy, both in environmental and financial terms, there is a need to achieve higher efficiency in motor drive systems and to reduce the cost of operating and production.
Renesas' low-voltage motor drive solution addresses the key requirements for consumer appliances due to their safety, smaller form factor, optimized cost, and unified DC-link bus shared with other electronic circuits, and it brings the following advantages:
- Higher safety margins - Isolating the motors, pumps, and fans from the mains voltage level makes systems safer for designers and maintenance staff.
- Reduced size and cost - High voltage IGBT, MOSFET, or Integrated Power Modules (IPMs) usually need an isolated 12Vdc ~ 15Vdc or an external bootstrap circuit to turn on the gates, which increases the number of components, and the production cost of such drive boards. On the contrary, the low-voltage solutions significantly reduce the PCB size and cost by using internal bootstrap and enjoying lower creepage and clearance requirements together.
- Improved motor drive efficiency - In low-voltage low-power applications, MOSFETs with a small RDSon and gate charge achieve very low losses which may not require extra heat-dissipation components, contributing more towards overall system cost reduction.
To enhance the motor control performance and achieve the highest efficiency while keeping the cost of production and development as low as possible, choosing the right microcontroller is the key decision factor. Renesas MCUs are designed specifically for motor control applications to offer simpler hardware design by integrating analog and digital peripherals and faster software development via state-of-the-art software development kits (SDKs). We will explain the unique features of these MCUs in detail and how they will lead to the best low-voltage motor drive system designs.
Low Voltage Motor Control Trends & Key Challenges
A microcontroller executing the motor control algorithm relies on several feedback measurements, filtering, and mathematical calculations to efficiently deliver the required torque and speed; thus, several analog electronic circuitries are required to convert the sensors’ outputs to a proper voltage level for the MCU and enable reliable protection. The rich integrated analog and digital peripherals of the RA6T2, RX13T, RX26T, and RX72T MCUs combined with a Renesas proprietary core and powerful Arm® Cortex®-M cores, as well as Renesas’ exclusive IIR filter and trigonometric function accelerators (IIRFA and TFU), make these MCUs the perfect choice to tackle the most common design challenges.
Current Measurement
The most common way to measure current in low-voltage drives is to sense the voltage drop across a shunt or current sense resistor. The selection of a very small resistor yields lower power losses but substantially reduces the sense voltage magnitude and makes it impossible for an ADC to read the value. To address this common issue, Renesas introduces 12 or 16-bit ADCs with sample and hold and an embedded programmable gain amplifier (PGA) to precisely amplify the input signal and inject stable DC-offset before converting it to a digital value. Using the internal PGA eradicates the external components and reduces the size and cost of the PCB while offering low noise and stable reference voltage operation with the ability to compensate for temperature variations.
Overcurrent Protection
It is imperative to protect the drive system and motor in case of high inrush currents as fast as possible, which is usually implemented by external analog comparators to shut down the gate drives. However, the RA6T family of 32-bit MCUs offers an integrated high-speed analog comparator (ACMPHS) to compare the PGA output against the maximum level and turn off the PWM signals with a delay of less than 50 nanoseconds.
Measurement Noise
The high-frequency switching ripple induced by the inverter and environmental white noise undermine the quality of measured voltage and currents; hence, filtering the signals is necessary. Instead of bulky and unstable external analog low pass filters, Renesas’ RA6Tx MCU offers a hardware-implemented biquad IIR filter accelerator (IIRFA) to reduce the processing cycles in speed control and current loop calculations by about 40% compared to other MCUs.
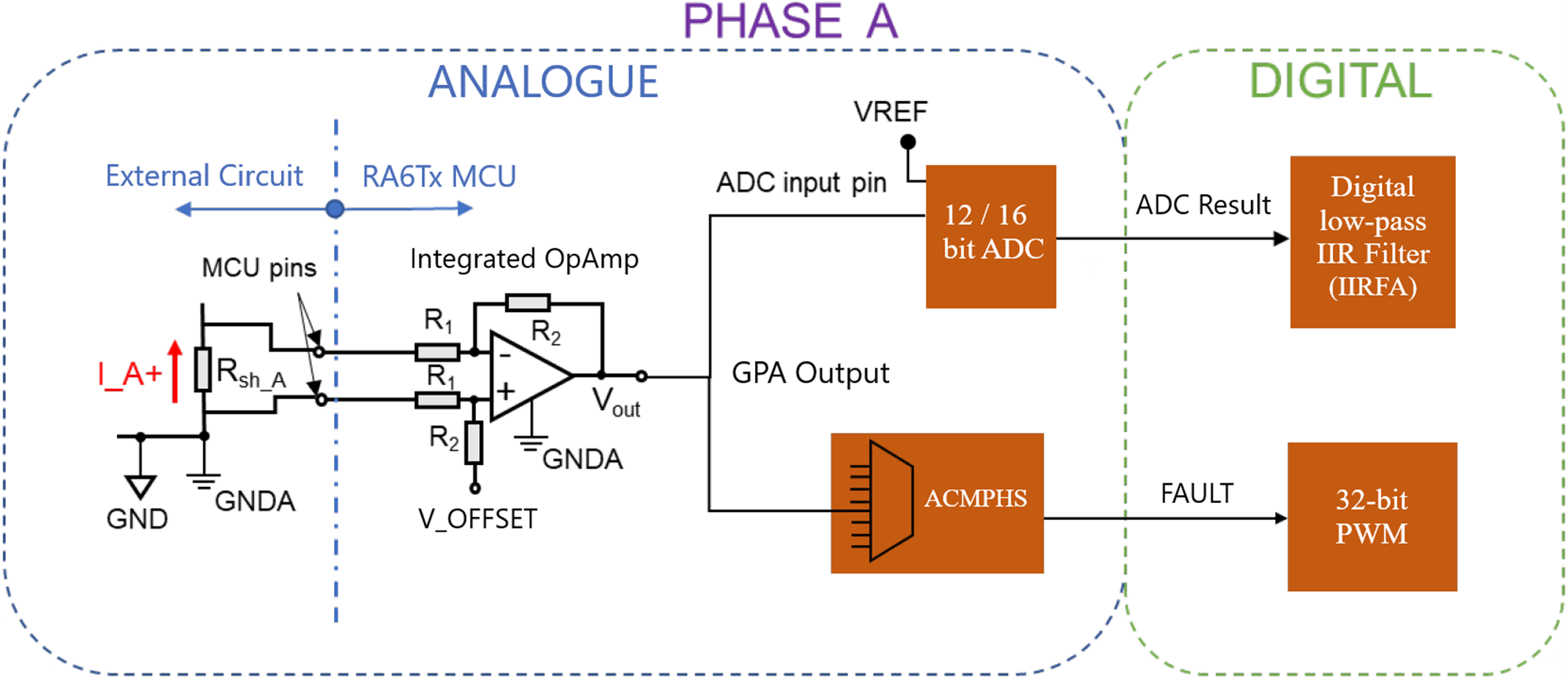
Figure 1. Application of Renesas' RA6Tx Rich Integrated Analog Peripherals for a 3-Phase BLDC Drive
(Includes Phase A Only)
Efficient Method to Control BLDC
Along with the mixed analog-digital hardware required for BLDC drive, the control algorithm must deliver maximum efficiency to reduce production and operating costs for manufacturers and end users. There are several different control methods employed for BLDC motors, each with its own set of principles and applications. The most commonly used methods include trapezoidal control, sinusoidal control, field-orientated control (FOC), and vector control.
Trapezoidal Control
Trapezoidal control is the simplest form of BLDC motor control which operates by applying voltage to the motor's windings in a six-step commutation pattern based on Hall sensor feedback. This method offers low-cost implementation while providing good performance in high-speed applications such as fans or pumps. The main disadvantage of this method is its inability to produce smooth torque output, due to the six-step commutation, resulting in increased audible noise and vibration during operation.
Sinusoidal Control
By controlling the phase current's sine-wave shape through PWM techniques based on rotor position sensors data or back-EMF estimation algorithms, better performance can be achieved, compared to the trapezoidal method, across a wider range of speeds, resulting in smoother operation at lower speeds suitable for high power motors/compressors. However, this method does not guarantee the optimal use of the electromagnetic capabilities of the motor and fails to offer maximum efficiency.
Field-Orientated Control
Field-oriented control (FOC) is a more advanced technique that decouples the torque-producing component from the magnetizing component within the motor flux vector space. By aligning rotor magnetic flux with stator magnetic flux, higher levels of controllability can be achieved leading to improved dynamic response and high torque capabilities, making it an ideal method for demanding applications over a wide speed range from standstill to rated. Modeling the motor in a complex plane allows for precise control of both torque and flux components by manipulating the magnitude and phase angle of the current vectors on a rotating coordinate system known as the dq-reference frame. By manipulating the magnitude and phase of these vectors, vector control achieves precise regulation of torque and flux components, leading to superior performance in terms of efficiency, dynamic response, and smooth output torque.
Vector Control
Vector control (VC) is a further refinement of FOC where the motor model is represented in a complex plane. It allows for precise control of both torque and flux components by manipulating the magnitude and phase angle of the current vectors on a rotating coordinate system known as the dq-reference frame. By manipulating the magnitude and phase of these vectors, vector control achieves precise regulation of torque and flux components, leading to superior performance in terms of efficiency, dynamic response, and smooth output torque.
Maximum Torque per Ampere
Both brushless direct current motors (BLDC) and permanent magnet synchronous motors (PMSM) can benefit from the concept of maximum torque per ampere (MTPA) to optimize motor operation by adjusting current levels to achieve maximum electromagnetic efficiency. By operating at or near the peak power point on the motor's torque-speed characteristic curve, the vector control-based MTPA strategy enables improved energy conversion while reducing losses.
The MTPA algorithm and dq-frame transformations require complex trigonometric functions to be calculated at every control sampling time. The industry-leading trigonometric function unit (TFU) hardware accelerator developed by Renesas leads to a 20% lower processing time and smaller ROM size compared with the lookup table on Flash memory.
Figure 2. Maximum Torque per Ampere Trajectory [Courtesy of “Modern Power Electronics and AC Drives”, B. Bose, Prentice Hall, 2001]
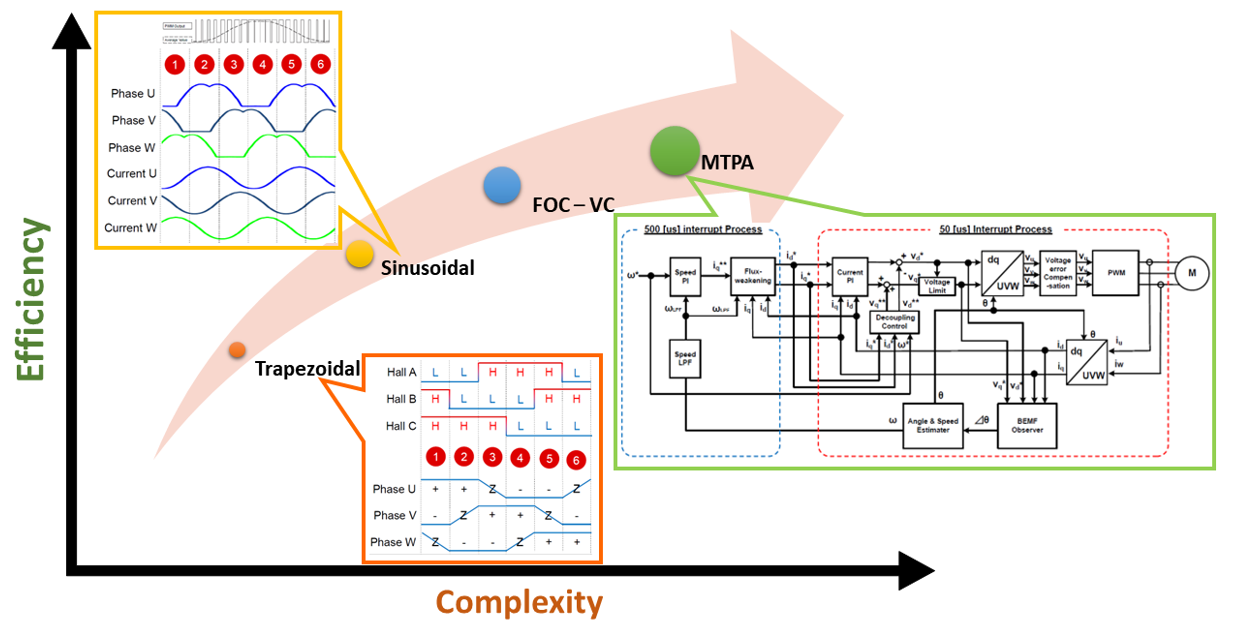
Figure 3. Comparison of BLDC Control Methods
Accelerate Your Low-Voltage BLDC Drive Design with Renesas
Motor-based embedded system development can be quite challenging especially as it relates to optimizing the control of motor drives to achieve required performance and efficiency. However, the right software and hardware design tools can help accelerate development time. Renesas offers a wide range of motor control devices based on the RL78, RX, and RA MCU families and related reference designs and starter kits to accelerate your motor control designs. Here, we would like to share one of the examples from our RA MCU portfolio, the Renesas Solution Starter Kit (RSSK) for RA & RX-based Motor Control Evaluation System, offering a comprehensive solution platform. It provides a low-voltage BLDC drive solution that facilitates the evaluation of motor control with various sample codes and application notes to help reduce time to market. In addition, Renesas provides the Motor Workbench which is a complete development environment including a debugging tool with the Analyzer function that can read and write variables inside the MCU and display the waveform of variables within an intuitive GUI.
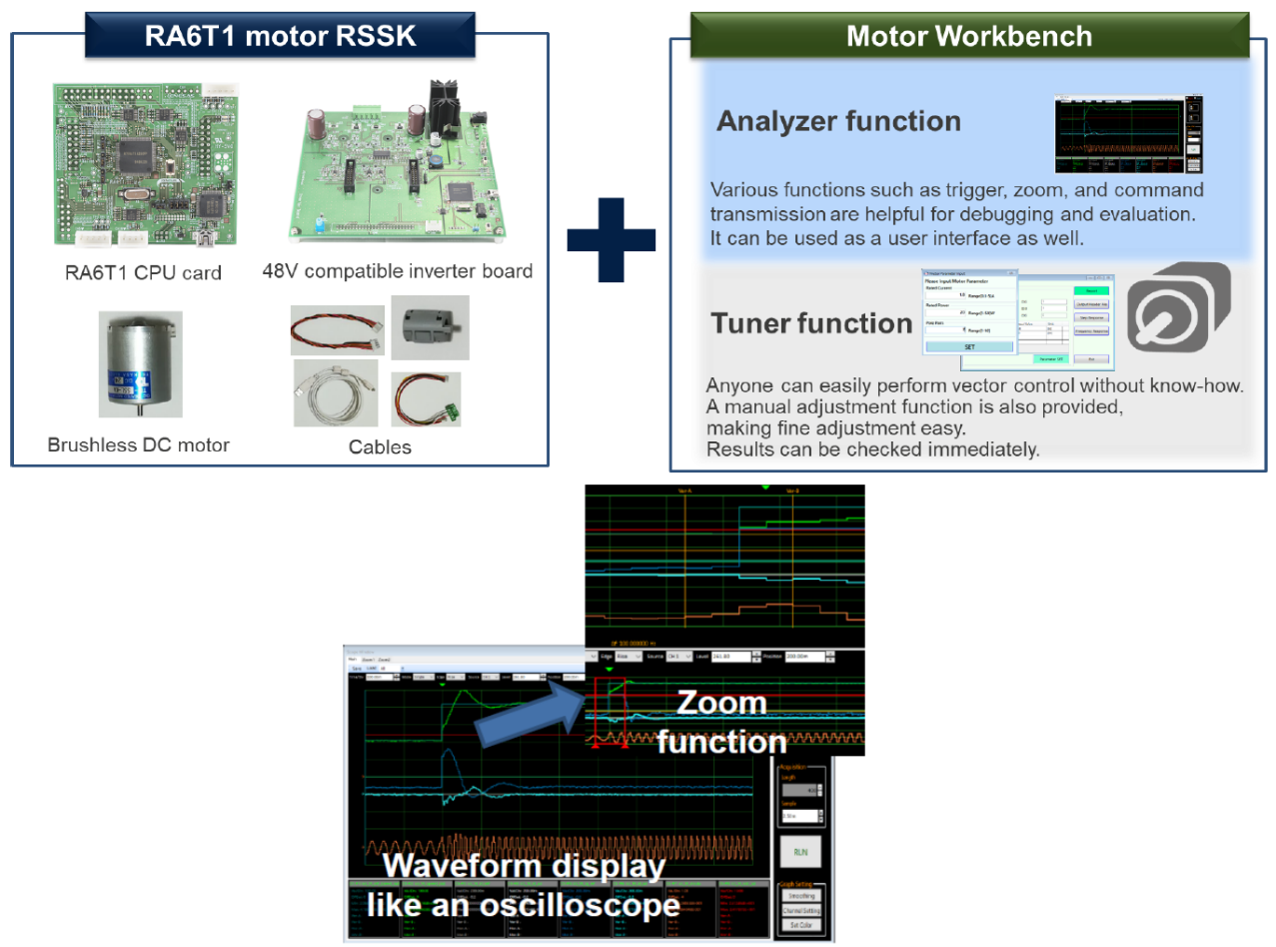
Figure 4. Renesas Motor Control Evaluation System for RA6T Family of MCUs
The consumer appliance industry and other related low-voltage motor-based applications are rapidly shifting towards using highly efficient BLDC motors and associated drive systems instead of obsolete line-driven universal AC motors. Reducing the power consumption, physical size, and overall design cost remains some of the key challenges in this fast-evolving industry. Hence, the selection of the best microcontroller and power components is of utmost importance to ensure the deployment of a competitive end product. Renesas, a market leader in this domain offers a wide range of MCUs, specifically tailored for motor drive applications with highly integrated analog peripherals and powerful processing ability to help embedded developers achieve the most effective control implementation. Using Renesas’ cutting-edge BLDC development platforms coupled with the freely available integrated IDE workbench and software examples enables designers to accelerate the delivery of their final products without any compromise.