If you are measuring fluid flow, chances are you have come across or are using a turbine-type mechanical flow meter. These mechanical types of fluid metering have worked well for most applications so why is there a drive to replace them?
To answer this, let’s take a quick look at how these turbine meters work. The rotor rotates as the fluid passes through the flow channel housing and a pickup sensor detects the rotor blade as it spins. There are different types of pickup sensors, including Hall Effect and inductance. The flow rate is proportional to the frequency of these pulses detected.
There are advantages to using turbine flow meters, including cost and simplicity. Emerging applications, however, are requiring higher accuracy and better long-term robustness. Systems are now integrated with more functionality into the same or smaller enclosures than these basic solutions can provide.
A recent conversation I had with a customer illustrates this point well. This engineer emphasized that they cannot position these turbine types of meters close to the actual pump because the magnetic field will cause the meter to function improperly. There are limitations to where and how these meters are mounted in order to operate within specifications.
To address these problems and advance flow sensing technology, Renesas utilizes a solid-state MEMS flow sensor without moving, mechanical components that can wear down over time and that will remain stable over wide operating temperatures. Without any obstructive components, the risk of clogging the flow path is very low to none. The elimination of moving parts ensures a consistent and maintenance-free operation with long-term stability.
In an application specific to the beverage dispensing equipment, one very important but not widely known requirement is the ability to clean the passages of the flow meter. Turbine-type meters cannot be thoroughly cleaned and residues form over time. With a MEMS sensor, even though the sensor element itself should not be touched by mechanical means, water-based detergents do a sufficient job of cleaning and disinfecting.
Another issue worth mentioning is that when fluid flow exhibits turbulent and/or oscillating behavior, a turbine meter may hesitate and accuracy will suffer, whereas with instantaneous response time — only a few milliseconds — the MEMS sensor can react accordingly. Similarly, bubbles in the fluid can be detected and digitally compensated to minimize any impact on the measurement.
MEMS-based flow sensors have already made inroads into fluid flow metering systems. With the FS2012 family of flow sensors, Renesas makes it easier to replace the familiar mechanical-type meters by featuring an analog output and advancing it with a digital I2C output, along with a low operating supply voltage (5V DC).
For more information, including datasheets and evaluation kits, please visit renesas.com/flowsensors.
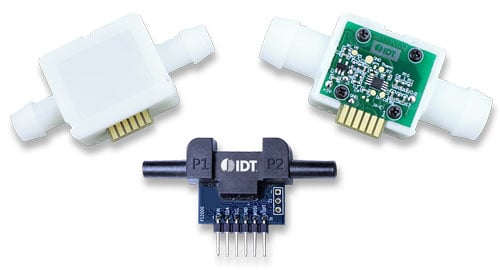